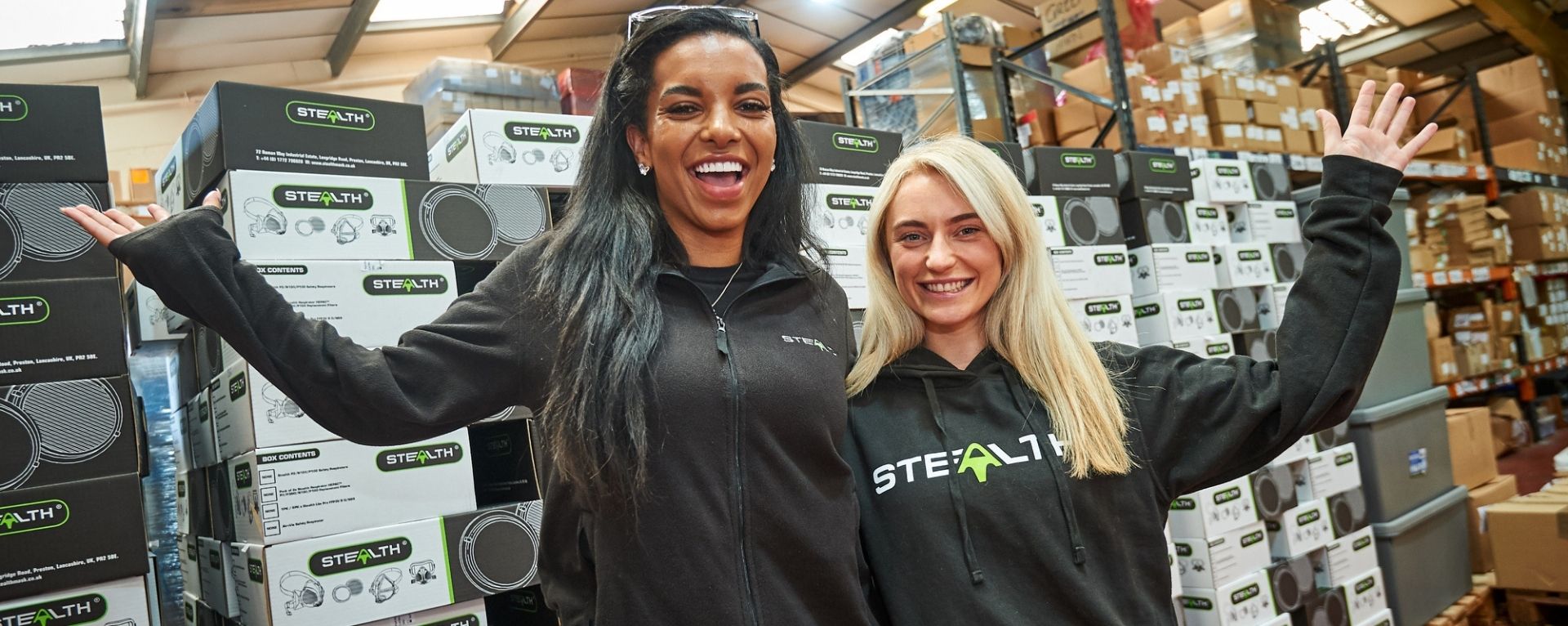
Stealth Mask develops new transparent face mask
Stealth Mask, the UK-based manufacturer of professional grade face masks and filters – and Sugar PR client – is expanding as global demand for personal protective equipment (PPE) continues to soar.
Lancashire-based Stealth Mask was founded in 2017 as a spinout from Air Filtration Solutions, which designs and manufactures air filters which reduce and capture contaminants in medical devices.
Since then, it has sold more than 5 million professional-grade face masks and now exports its products to 22 countries including the USA, Australia, New Zealand, Canada and Germany.
The family-owned business now employs 120 people at 8,000 sq. ft headquarters in Preston, Lancashire and is moving to a larger site in the city next year as it continues to grow its range of products and services in the PPE sector.
Clients include the NHS, Screwfix, Toolstation and Howdens. Stealth Mask’s own range of eight certified products are used daily on construction sites, hospitals, farms and industrial premises all over the world.
It’s latest product, the Clarity FFP3, – which is making headlines – and continues to do so – here, here and here – features a transparent anti-fog window to aid communication between colleagues. It also breaks down emotional barriers between care staff and vulnerable patients. It was developed following reports by clinicians that traditional face masks make it challenging to communicate clearly with colleagues, elderly patients or people with learning disabilities, hearing impairments or other more complex care requirements.
Clarity is the first transparent FFP3 face mask in the market in the UK, which means it has a minimum total filtration efficiency of 99% and low breathing resistance when in use. The company expects demand to be high as public and private sector healthcare organisations focus on becoming more accessible and inclusive in their services to deliver better clinical outcomes.
(Stealth’s new transparent face mask is aimed at enhancing communication and inclusivity between clinical colleagues, care staff and patients)
Karl Howard, Managing Director of Stealth Mask, said:
“Our masks are aimed at protecting users from harmful contaminants in their professional working environment – whether that’s a construction site, an industrial plant or a hospital. The pandemic has highlighted to large organisations the importance of accessing PPE to protect their employees from harm.
“It’s also driven innovation in the sector and its why we’ve now launched our new transparent facemask which we firmly believe will become the new standard in terms of FFP3 face masks in care and medical settings. The human advantages it brings in terms of better communication between healthcare staff and patients at a time when people are at their most vulnerable or emotional and need it the most is what is urgently needed now.
“Getting the right balance between maximising the size of the transparent window to easily see facial expressions and protecting the user with the highest level of protection has taken almost a year of research and development, including working alongside the Allied Health Research Unit at the University of Central Lancashire (UCLAN) and focus groups with keyworkers from a range of sectors.
“We’re pleased to have developed it all here in the United Kingdom and we’re proud to be setting new standards in terms of accessible and inclusive PPE equipment.
“Face masks have obviously become a major talking point during the past 18 months but the fact remains that their use in a professional or healthcare environment will remain and standards and designs will continue to evolve. We’re really proud to be a family-owned manufacturer in the heart of Lancashire with good products that are being used by professionals all over the world.”
David Wood, Sales Director at Stealth Mask, said:
“We’ve been in the face mask business since well before the pandemic started so we’ve had a head start on research and development compared to newcomers in the market. Our heritage of designing and developing air filters to the medical sector also gives us a tremendous advantage and the fact that we’re making them here in the United Kingdom, in the heart of Lancashire, is a sign of trust and quality to the rest of the world.
“During the peak of the pandemic, we were shipping out 100,000 face masks a week, not just to large organisations but to small businesses and consumers too. Since then, public and private sector organisations around the world have established more robust procurement methods to ensure that they aren’t caught short for PPE equipment and facemasks in particular for their employees.
“This has driven up standards and created a demand for professionally certified facemasks and filters which offer the highest levels of protection for employees in settings where facemasks are required.”